Weights
Paper density (also known as basis weight and grammage) is a term used in the pulp and paper industry and also for fabric industry to denote a measure of mass of the product per unit of area for a type of fabric, paper or papernoard. The term "density" is not used in its traditional sense of mass per unit volume.
"Paper density", rather, is a measure of the area density. Paper products that let little or no light pass through (e.g. poster board) are considered dense or heavy. Paper products that allow some light to pass through (e.g. tissue paper) are considered lightweight.
In the pulp and paper industry, it is common to set a commercial paper machine to produce paper to a target paper density. Paper density can also be used to distinguish paper from paperboard as the latter usually has a grammage greater than 134 g/m².
Two ways of expressing paper density are commonly used:
Two ways of expressing paper density are commonly used:
Expressed in grams per square meter (g/m²), paper density is also known as grammage. This is the measure used in most parts of the world.
Expressed in terms of the mass (expressed as weight) per number of sheets, it is known as basis weight. The convention used in the United States and a few other countries using US paper sixes is pounds of a ream of 500 (or in some cases 1000) sheets of a given (raw, still uncut) basis size. Japanese paper is expressed as the weight in kg of 1000 sheets.
Caliper
Caliper is usually measured in micrometers (1/1000 of a mm), or in the United States also in mils. (1 mil = 0.001 inch = 25.4 µm)
Typically grammage is measured in paper mill on-line by Quality Control System and verified by laboratory measurement.
GSM
I know that it’s not easy to visualise a square metre of paper. So here’s a basic layman’s translation of some of the most common paperweights.
- 350GSM – This is what you might expect a reasonable quality business card to be printed on.
- 180 to 250 GSM – Like a mid-market magazine cover.
- 130 to 170 GSM – A good quality promotional poster. Something that you’d expect to last a couple of months in most conditions.
- 90GSM – Mid-Market magazine inner pages
- 35 to 55 GSM – Most newspapers
- Less than 35 GSM – If someone’s trying to sell you this as anything other than rice paper, you want to be reporting them for attempted theft.
Metric Vs Imperial
Paper Sizes
Many paper size standards conventions have existed at different times and in different countries. Today there is one widespread international ISO standard (including A4, B3, C4, etc.) and a local standard used in North America (including letter, legal, ledger, etc.). The paper sizes affect writing paper, stationary, cards, and some printed documents. The standards also have related sizes for envelopes.
The ISO paper size system, the height-to-width ratio of all pages is the square root of two (1.4142 : 1).
In other words, the width and the height of a page relate to each other like the side and the diagonal of a square. This aspect ratio is especially convenient for a paper size. If you put two such pages next to each other, or equivalently cut one parallel to its shorter side into two equal pieces, then the resulting page will have again the same width/height ratio.
The diagram helps explain this better with exact measurements.
A Sizes
B Sizes
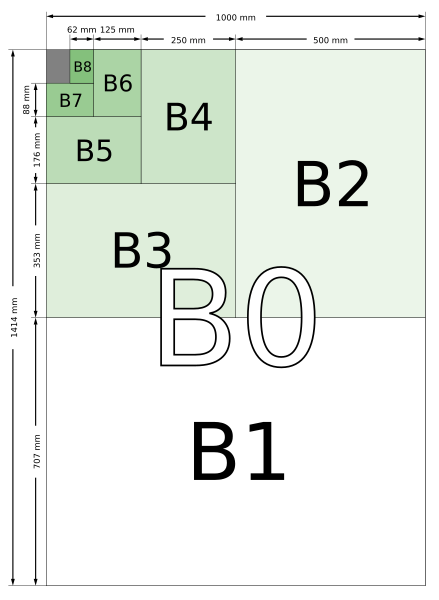
In addition to the A series, there is a less common B series. The area of B series sheets is the geometric mean of successive A series sheets. So, B1 is between A0 and A1 in size, with an area of 0.707 m2 (

The B series is also used for envelopes and passports. The B-series is widely used in the printing industry to describe both paper sizes and printing press sizes, including digital presses. B3 paper is used to print two US letter or A4 pages side by side using imposition; four pages would be printed on B2, eight on B1, etc.
The C series is used only for envelopes and is defined in ISO 269. The area of C series sheets is the geometric mean of the areas of the A and B series sheets of the same number; for instance, the area of a C4 sheet is the geometric mean of the areas of an A4 sheet and a B4 sheet. This means that C4 is slightly larger than A4, and B4 slightly larger than C4. The practical usage of this is that a letter written on A4 paper fits inside a C4 envelope, and a C4 envelope fits inside a B4 envelope.
One of the most widely used business envelopes, the DL format does not fall under the C series sizes as it has a different aspect ratio. This envelope originated in Germany in the 1920's and was known as DIN Lang, but DL is now more commonly expanded to 'Dimension Lengthwise'. This size is defined in the ISO standards for envelope sizes, as the standard would have been remiss in omitting the most commonly used business envelope size.
The dimensions of DL are 110 x 220 mm (4⅓" x 8⅔") and as such the DL envelope will hold an A4 sheet of paper folded into 3 equal sections parallel to its shortest sides.
Despite complaints from manufacturers of automatic enveloping machines that it is slightly too small for reliable enveloping and the introduction of a C6/5 envelope at 114 x 229 mm, the original DL size continues to be most commonly used.
Broadsheet Size
Dimensions: 750 x 600 mm (29.5" x 23.5")
The term broadsheet derives from single sheets of political satire and ballads sold on the streets, which became popular after the British placed a tax on newspapers by the number of pages in 1712.
The broadsheet size for newspapers is becoming less popular and many titles are switching from broadsheet to tabloid.
In Australia and New Zealand the term broadsheet is used to refer to papers that are printed on A1 size paper (841 x 594 mm - 33.1" x 23.4").
Berliner
Dimensions: 470 mm × 315 mm (18.5" × 12.4")
The Berliner format (also known as Midi) is commonly used by newspapers across Europe. Confusingly the title 'Berliner Zeitung', often referred to as just 'Berliner' is not printed in berliner size.
Tabloid Size
Dimensions: 430 x 280 mm (16.9" x 11.0")
The tabloid size is often referred to as being 'half the size of a broadsheet' however this is not strictly true as broadsheet is 750 x 600 mm (29.5" x 23.5")
Tabloid size is actually not very different from A3 and thus a transition to printing tabloids on an A2 sheet (remember that newspaper sizes are the size of the folded pages) would be sensible in the longer term.
The word tabloid when referring to newspaper sizes comes from the style of journalism known as 'tabloid journalism' that compacted stories into short, easy to read and often exaggerated forms. Tabloid journalism itself got its name from the 'tabloid pills' marketed in the 1880's, that were the first highly compacted and easy to swallow pills commonly available.
The tabloid size is widely used across the globe these days, with titles in the US, Russia, China, the UK, Canada, Australia, Brazil and many other countries using this format. Recently many established papers have changed from broadsheet size to tabloid size as it has proved more popular with readers.
Compact Size
This size is the same as tabloid. The term being coined when the 'quality' or 'high brow' press titles moved from the traditional broadsheet size to the smaller tabloid size, as they didn't want to be associated with the sensationalism of tabloid journalism.
ANSI sizes
In 1996, the American NAtional Standards Institute adopted ANSI/ASME Y14.1 which defined a regular series of paper sizes based upon the de facto standard 81⁄2 in × 11 in (215.9 mm × 279.4 mm) "letter" size which it assigned "ANSI A". This series also includes "ledger"/"tabloid" as "ANSI B". This series is somewhat similar to the ISO standard in that cutting a sheet in half would produce two sheets of the next smaller size. Unlike the ISO standard, however, the arbitrary aspect ratio forces this series to have two alternating aspect ratios. The ANSI series is shown below.
With care, documents can be prepared so that the text and images fit on either ANSI or their equivalent ISO sheets at 1:1 reproduction scale.
Current standard sizes of U.S., Canadian and Mexican paper are a subset of the traditional inch-based sizes described below. "Letter", "legal", "ledger", and "tabloid" are by far the most commonly used of these for everyday activities. The origins of the exact dimensions of "letter" size paper (81⁄2 in × 11 in or 215.9 mm × 279.4 mm) are lost in tradition and not well documented. The American Forest and Paper Association argues that the dimension originates from the days of manual paper making, and that the 11 inch length of the page is about a quarter of "the average maximum stretch of an experienced vatman's arms." However, this does not explain the width or aspect ratio. Outside of North America, Letter size is also known as "American Quarto"and the size is indeed almost exactly a quarter of the old Imperial (British) paper size known as Demy 4to (17½"×22½"), allowing ½" for trimming.
Finishes
Cockle
This is often found in bond paper and has a rippled, puckered surface. Looking more like hand made paper it is created by air drying paper with a controlled amount of tension.
C Sizes
DL
The dimensions of DL are 110 x 220 mm (4⅓" x 8⅔") and as such the DL envelope will hold an A4 sheet of paper folded into 3 equal sections parallel to its shortest sides.
Despite complaints from manufacturers of automatic enveloping machines that it is slightly too small for reliable enveloping and the introduction of a C6/5 envelope at 114 x 229 mm, the original DL size continues to be most commonly used.
Broadsheet Size
Dimensions: 750 x 600 mm (29.5" x 23.5")
The term broadsheet derives from single sheets of political satire and ballads sold on the streets, which became popular after the British placed a tax on newspapers by the number of pages in 1712.
The broadsheet size for newspapers is becoming less popular and many titles are switching from broadsheet to tabloid.
In Australia and New Zealand the term broadsheet is used to refer to papers that are printed on A1 size paper (841 x 594 mm - 33.1" x 23.4").
Berliner
Dimensions: 470 mm × 315 mm (18.5" × 12.4")
The Berliner format (also known as Midi) is commonly used by newspapers across Europe. Confusingly the title 'Berliner Zeitung', often referred to as just 'Berliner' is not printed in berliner size.
Tabloid Size
Dimensions: 430 x 280 mm (16.9" x 11.0")
The tabloid size is often referred to as being 'half the size of a broadsheet' however this is not strictly true as broadsheet is 750 x 600 mm (29.5" x 23.5")
Tabloid size is actually not very different from A3 and thus a transition to printing tabloids on an A2 sheet (remember that newspaper sizes are the size of the folded pages) would be sensible in the longer term.
The word tabloid when referring to newspaper sizes comes from the style of journalism known as 'tabloid journalism' that compacted stories into short, easy to read and often exaggerated forms. Tabloid journalism itself got its name from the 'tabloid pills' marketed in the 1880's, that were the first highly compacted and easy to swallow pills commonly available.
The tabloid size is widely used across the globe these days, with titles in the US, Russia, China, the UK, Canada, Australia, Brazil and many other countries using this format. Recently many established papers have changed from broadsheet size to tabloid size as it has proved more popular with readers.
Compact Size
This size is the same as tabloid. The term being coined when the 'quality' or 'high brow' press titles moved from the traditional broadsheet size to the smaller tabloid size, as they didn't want to be associated with the sensationalism of tabloid journalism.
In 1996, the American NAtional Standards Institute adopted ANSI/ASME Y14.1 which defined a regular series of paper sizes based upon the de facto standard 81⁄2 in × 11 in (215.9 mm × 279.4 mm) "letter" size which it assigned "ANSI A". This series also includes "ledger"/"tabloid" as "ANSI B". This series is somewhat similar to the ISO standard in that cutting a sheet in half would produce two sheets of the next smaller size. Unlike the ISO standard, however, the arbitrary aspect ratio forces this series to have two alternating aspect ratios. The ANSI series is shown below.
With care, documents can be prepared so that the text and images fit on either ANSI or their equivalent ISO sheets at 1:1 reproduction scale.
North American Sizes
Current standard sizes of U.S., Canadian and Mexican paper are a subset of the traditional inch-based sizes described below. "Letter", "legal", "ledger", and "tabloid" are by far the most commonly used of these for everyday activities. The origins of the exact dimensions of "letter" size paper (81⁄2 in × 11 in or 215.9 mm × 279.4 mm) are lost in tradition and not well documented. The American Forest and Paper Association argues that the dimension originates from the days of manual paper making, and that the 11 inch length of the page is about a quarter of "the average maximum stretch of an experienced vatman's arms." However, this does not explain the width or aspect ratio. Outside of North America, Letter size is also known as "American Quarto"and the size is indeed almost exactly a quarter of the old Imperial (British) paper size known as Demy 4to (17½"×22½"), allowing ½" for trimming.
Finishes
Cockle
This is often found in bond paper and has a rippled, puckered surface. Looking more like hand made paper it is created by air drying paper with a controlled amount of tension.
Felt
This is uncoated paper whose soft surface texture is created by pressing patterned woven wool or synthetic felt belts onto the paper during manufacture.
Gloss
This lustrous, shiny, surface is produced by adding compounds to the paper during its manufacture. It is usually found on higher quality coated paper.
This lustrous, shiny, surface is produced by adding compounds to the paper during its manufacture. It is usually found on higher quality coated paper.
Laid
It simulates the look and feel of handmade paper containing grids of parallel lines and is created using special rollers applied while the paper is still wet.
It simulates the look and feel of handmade paper containing grids of parallel lines and is created using special rollers applied while the paper is still wet.
Linen
This looks like linen cloth and is an embossed finish.
This looks like linen cloth and is an embossed finish.
Matt
This is a dull finish devoid of the luster of gloss finishes making text easier to read and colours looking softer.
This is a dull finish devoid of the luster of gloss finishes making text easier to read and colours looking softer.
Parchment
When treating paper with sulfuric acid it creates this antique appearance and becomes grease and dirt resistant as well as having a high wet-strength.
When treating paper with sulfuric acid it creates this antique appearance and becomes grease and dirt resistant as well as having a high wet-strength.
Smooth
This smooth finish is achieved via calendaring.
This smooth finish is achieved via calendaring.
Vellum
This is a slightly rough, “toothy” textured finish looking similar to an eggshell. It works well in high-speed printing and has a very high ink absorbency rate.
This is a slightly rough, “toothy” textured finish looking similar to an eggshell. It works well in high-speed printing and has a very high ink absorbency rate.
Wove
This smooth but not slick finish has a slightly patterned mesh texture created via a felt roller covered in woven wire.
This smooth but not slick finish has a slightly patterned mesh texture created via a felt roller covered in woven wire.
Paperboard
This is a thick paper based material. While there is no rigid differentiation between paper and paperboard, paperboard is generally thicker (usually over 0.25 mm/0.010 in or 10 points) than paper. According to ISO standards, paperboard is a paper with a basis weight (grammage) above 224 g/m2, but there are exceptions. Paperboard can be single or multi-ply. Paperboard can be easily cut and formed, is lightweight, and because it is strong, is used in packaging. Another end-use would be graphic printing, such as book and magazine covers or postcards. Sometimes it is referred to as cardboard, which is a generic, lay term used to refer to any heavy paper pulp based board.Cellulose Acetate film, or safety film, is used inphotography as a base material for photographic emulsions. It was introduced in the early 20th century by film manufacturers as a safe film base replacement for unstable and highly flammable nitrate film.
Binding
Bookbinding is the process of physically assembling a book from a number of folded or unfolded sheets of paper or other material. It usually involves attaching a book cover to the resulting text-block.
The video above demonstrates most of the different binding and finishing techniques.
The video above demonstrates most of the different binding and finishing techniques.
Saddle Stitch Binding
A book stapled at the center two or three times is nothing but saddle stitched. The saddle refers to the center of the folded papers where it is stapled, which is why saddle stitch binding is one of the most common an popular methods of book binding.
You can also staple from one side of the book if you don't prefer center stapled books. A long arm stapler is enough to start saddle stitchig your books.
Paperback Binding
Paper back binding is fairly simple, and you can bind paperback books at home after learning the process. Many people have found this useful and use this book binding style to do it by themselves.
Many authors who want to self publish but are not able to afford publishing houses, as well as book binding hobbyists who want to bind their own books, are using the paperback book binding method to bind their own books at home. Paperback binding is one of the more simple dyi book binding methods.
Hardcover Binding
Hardcover binding can also be done at home but it requires more effort. The different steps involved are making signatures, poking holes in the signatures, sewing (probably the hardest part of this style of book binding), making the cover, and finally attaching the cover to the stack of signatures.
The result of this style of binding is well worth the effort, as the final product is beautiful and will protect your projects.
Yotsume Toji Binding
This is also sometimes refereed to as Japanese STAB Stitch Binding.
In this binding four holes are made at one edge of the book. Then it is sewn in a particular to get the Yotsume Toji Binding. It is good for repairing books and to create your own small books.
This video shows how simple this kind of book binding method is to do...
Coptic Binding
Coptic binding is one of the oldest type of bookbinding which was practised by the Copts in Egypt. It is also simple and you can try it now itself.
In this binding there is no spine because of which the book can be folded so that both the covers touch each other and it will not be damaged.
Two covers are placed above and below the papers and it is sewed through one edge. There are different methods of sewing. Some of them are easy while others are difficult. I always advice to start with easy ones and then go for the difficult ones.
In this binding there is no spine because of which the book can be folded so that both the covers touch each other and it will not be damaged.
Two covers are placed above and below the papers and it is sewed through one edge. There are different methods of sewing. Some of them are easy while others are difficult. I always advice to start with easy ones and then go for the difficult ones.
This video below demonstrates how to achieve this method.
Thermal Tape
This is referred to as thermal binding, because it involves heat. Unlike the old form of hand taping that literally involved a piece of tape folded over the left edge of the sheets, modern “tape binding” has a nice professional finish.
Once cool the strip becomes firm so lettering can be applied to the spine. Spine Copy is printed using gold lettering. It is attractive and it makes your book easier to find on the shelf. Staple Bond Book
The Fastback is the most common machine used for this method of binding. Short video explains.
Perfect Bind
This is the traditional way of binding books. Paperbacks and encyclopedias are examples of the this type of binding.
Plastic Coil / Spiral
Little holes are punched down the left side of the pages and a plastic coil is run through them in a spiral pattern. Generally we keep black and white colored coils in stock, but other colors can be ordered in within a couple of business days.
A benefit of this binding is that it lays flat when opened.
This is referred to as thermal binding, because it involves heat. Unlike the old form of hand taping that literally involved a piece of tape folded over the left edge of the sheets, modern “tape binding” has a nice professional finish.
Once cool the strip becomes firm so lettering can be applied to the spine. Spine Copy is printed using gold lettering. It is attractive and it makes your book easier to find on the shelf. Staple Bond Book
The Fastback is the most common machine used for this method of binding. Short video explains.
Perfect Bind
This is the traditional way of binding books. Paperbacks and encyclopedias are examples of the this type of binding.
Plastic Coil / Spiral
Little holes are punched down the left side of the pages and a plastic coil is run through them in a spiral pattern. Generally we keep black and white colored coils in stock, but other colors can be ordered in within a couple of business days.
A benefit of this binding is that it lays flat when opened.
This video shows folding and creasing on an industrial level.
Examples of Binding
Collating
Diagram A
In printing, the term Collate refers to the gathering and arranging of individual sheets or other printed components into a pre-determined sequence. Basically, Collating creates consistent, logical sets from multiple parts.
Diagram A illustrates four sets of documents which have been collated. Diagram B illustrates four sets of documents which have not been collated.
Examples of Collated Documents
A short-run perfect bound book would require its pages to be collated in numerical order before it could be bound. Also, multi-part forms and checks are created from individual sheets collated in a specific sequence.
Diagram B
Diagram B - Uncollated sets of documents
Bear in mind that the individual parts of a print project can be collated without having to be bound or fastened together. For example, promotional packets – like those used for seminars, sales presentations, trade shows and other marketing purposes – are often collated in advance for easy distribution. Likewise, printed instructional handouts may be collated in a particular order but are not necessarily bound or fastened together.
Perforating
A perforation is a small hole in a thin material or web. There is usually more than one perforation in an organized fashion, where all of the holes are called a perforation. The process of creating perforations is called perforating, which involves puncturing the workpiece with a tool.
Perforations are usually used to allow easy separation of two sections of the material, such as allowing paper to be torn easily along the line. Packaging with perforations in paperboard or plastic film is easy for consumers to open. Other purposes include filtrating fluids, sound deadening, allowing light or fluids to pass through, and to create an aesthetic design.
Various applications include packaging films (to allow the contents to breathe), medical films, micro perforated plateand sound and vapour barriers.
Uses
Perforation frequently refers to the practice of creating a long series of holes or slits so that paper or plastics can be torn more easily along a given line: this is used in easy-open packaging.
Since the creation of perforation devices in the 1840s and 1850s, it has seen use in several areas.Postage Stamps are one common application of this, where small round holes are cut in lines to create individual pieces. Perforations on stamps are rather large, in the order of a millimeter, in comparison other perforated materials often have smaller holes.
It is common for notebooks and legal pads to have perforations making it easier to tear out individual pages. In today's cases, perforation is used in ways to separate loose leaf (or even a form of graph paper from a ringed binder). A fine perforation next to the rings allows the page to be separated from the book with no confetti.
Screwcaps on glass or plastic bottles are sealed with a ring at the bottom of the cap attached by perforation. Twisting the cap has the effect of rupturing the material between the perforations and indicating that the original seal has been broken.
Perforation can be created by pins, needles, die and punch or laser.
Perforated Edges on Stamps
Needle Punch
Perforated Notebook Edges
Creative Review - Perforated Subscription
Innovative Smirnoff Perfection Packaging
Food Carton
Shrinkwrapping
Shrink wrap, also shrinkwrap or shrink film, is a material made up of polymer plastic film. When heat is applied, it shrinks tightly over whatever it is covering. Heat can be applied with a hand held heat gun (electric or gas) or the product and film can pass through a heat tunnel a conveyor.
Leave your comment